„Die Beschäftigung mit Metallpulver war damals eine strategische Neuausrichtung und wir ein Stück weit Pioniere“, erinnert sich Emmelmann. Zunächst sei die Qualität der Metallbauteile nicht zufriedenstellend gewesen, doch Stück für Stück – oder Druck für Druck – habe sich das geändert. „Unser Ziel war es, die Technologie weiterzuentwickeln und sie parallel in die Industrie zu überführen.“ Erste Erfolge gab es im Bereich endoprothetischer Produkte, wie etwa Titanhüften oder -pfannen, auch aufgrund der Bionisierung der Funktionsbauteile. Dabei orientieren sich die Wissenschaftler*innen an der Natur – in diesem Fall dem menschlichen Knochenbau – und bilden sie nach. Der 3D-Druck zeigt hier eine seiner großen Stärken: Im Gegensatz zum konventionellen, also substraktiven Zerspanverfahren, erlaubt die additive Fertigung den Aufbau leichter und doch stabiler Hohlkörper. „Die ähnlich der „Spongiosa“ oberflächlich porös gefertigten Endoprothesen sind ausgesprochen passgenau, wachsen schneller ein, beschleunigen somit den Heilungsprozess und reduzieren die Krankenhausaufenthaltsdauer“, erklärt Emmelmann.
Ein wesentlicher Faktor für die Entwicklung von Zukunftstechnologien, wie den 3D-Druck, ist die Hochschulforschung und -lehre. Hamburg ist dabei gut aufgestellt. Die Hansestadt verzeichnet über 20 anerkannte private und staatliche Hochschulen, in der Metropolregion sind es sogar 36. Professor Dr.-Ing. Claus Emmelmann, Leiter des Instituts für Laser- und Anlagensystemtechnik (iLAS) an der Technischen Universität Hamburg (TUHH), wurde bereits vor 20 Jahren an die TUHH berufen, um unter anderem Rapid Prototyping – den Begriff 3D-Druck gab es damals noch nicht – von Kunststoff- auf Metallteile zu übertragen.
Bionisierung: Orientierung an der Natur
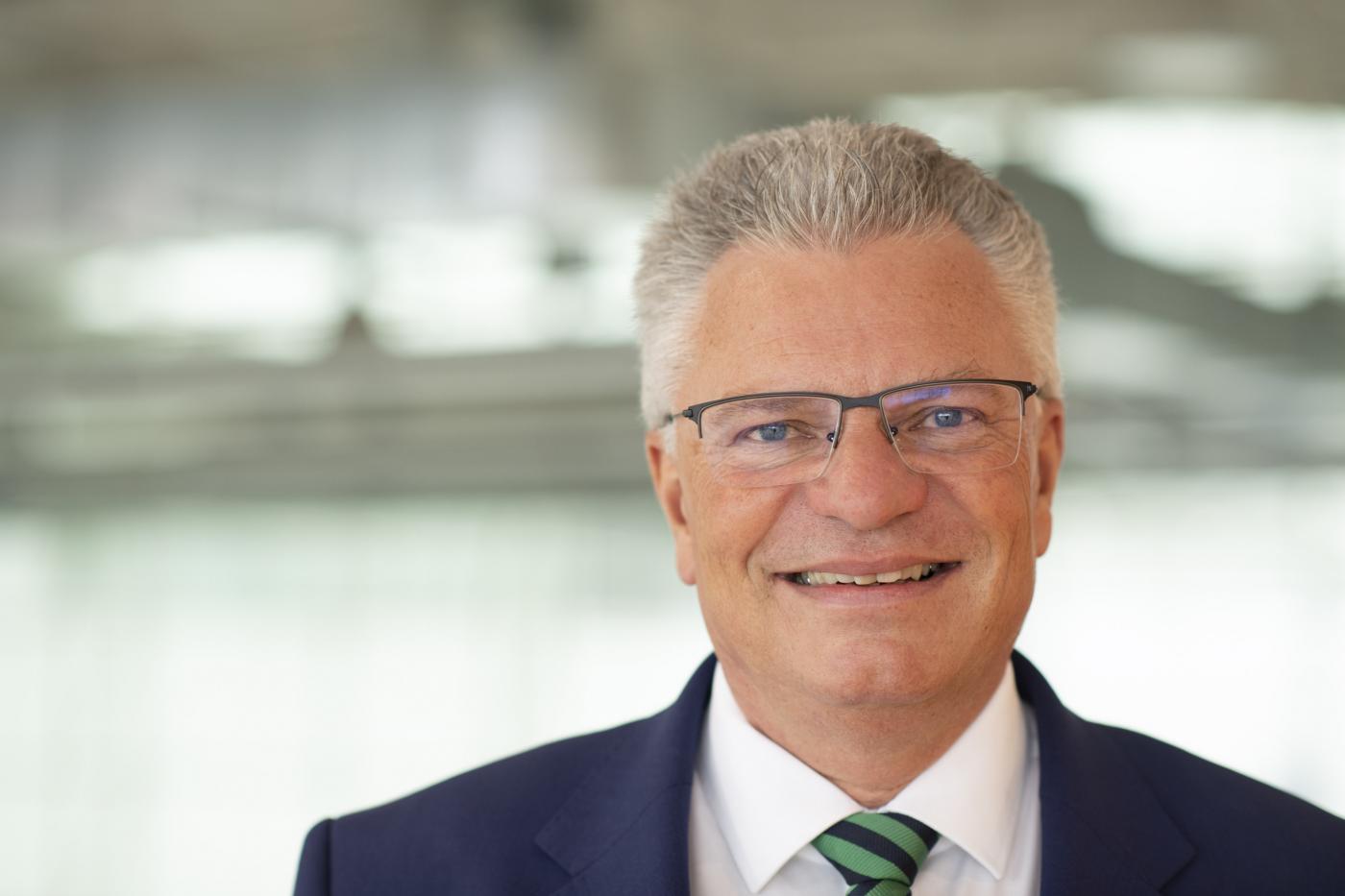
Ausgezeichnete Forschung
Ein weiterer Schlüsselfaktor: „Bauteile aus dem 3D-Drucker sind um bis zu 80% leichter als konventionell gefertigte Produkte – und somit von großem Interesse für den Flugzeugbau“, weiß Emmelmann. Gemeinsam mit den Partnern Airbus und Concept Laser entwickelte der Professor und sein Team im Forschungsprojekt „3D-Druck im zivilen Flugzeugbau - eine Fertigungsrevolution hebt ab“ einen Kabinenhalter aus Titan und wurde dafür ausgezeichnet. Inspiriert durch eine Vogelknochenstruktur und hergestellt im bionischen 3 D-Druck, konnte bei dem dreidimensionalen, hochbeanspruchbaren Bauteil aus Metall nahezu 50% des Gewichts eingespart werden. Das Forschungsteam gehörte damit Ende 2015 zum Kreis der besten 3 Innovationen für den Deutschen Zukunftspreis. Der Preis des Bundespräsidenten für Technik und Innovation wird für zukunftsweisende Ideen vergeben, die zur Marktreife entwickelt wurden und gehört zu den bedeutendsten Wissenschaftspreisen Deutschlands.
Forschung als Standortfaktor
„Das ist tatsächlich ein Preis von großer Strahlkraft, der somit Hamburg ins Rampenlicht gerückt hat, was wiederum das Interesse und Engagement seitens Politik und Industrie weiter befeuert hat“, betont Emmelmann. So wurde bereits 2009 die LZN Laser Zentrum Nord GmbH als Spin-Off des iLAS gegründet, die 2018 erfolgreich in die Fraunhofer-Gesellschaft als Fraunhofer-Einrichtung für Additive Produktionstechnologien IAPT, kurz Fraunhofer IAPT, eingegliedert wurde - immerhin eine der weltweit führenden Einrichtungen in der 3D-Druckforschung
Produkte neu denken
Ein weiterer wesentlicher Faktor für die Technologieentwicklung: Die Ausbildung von Fachkräften. Neben den Forschungsaktivitäten liegt ein zweiter Schwerpunkt des iLAS auf der Ausbildung von Ingenieuren und Berufsschullehrkäften in der Fachrichtung Metalltechnik. „Der 3D-Druck ist eine digitale und interdisziplinäre Technologie und findet sich somit in einem Großteil der von der Technischen Universität angebotenen Studiengängen“, erläutert Emmelmann. Praktisch ausprobieren lässt sich der 3D-Druck im FabLab der Hochschule. „Das wird von den Studierenden mit großer Begeisterung genutzt.“ Wichtig sei dabei die Chance zum Experimentieren, betont der Professor. „Es geht nicht darum, ein bestehendes Produkt auf eine neue Weise herzustellen, sondern grundlegend neu zu denken: Welche Produkte konnten bisher nicht oder nur mit großem Aufwand gefertigt werden? Welche neuen Möglichkeiten erschließt die Technologie? Ein solches Denken ist eine wichtige Voraussetzung für die nächste digital ausgerichtete industrielle Revolution.“
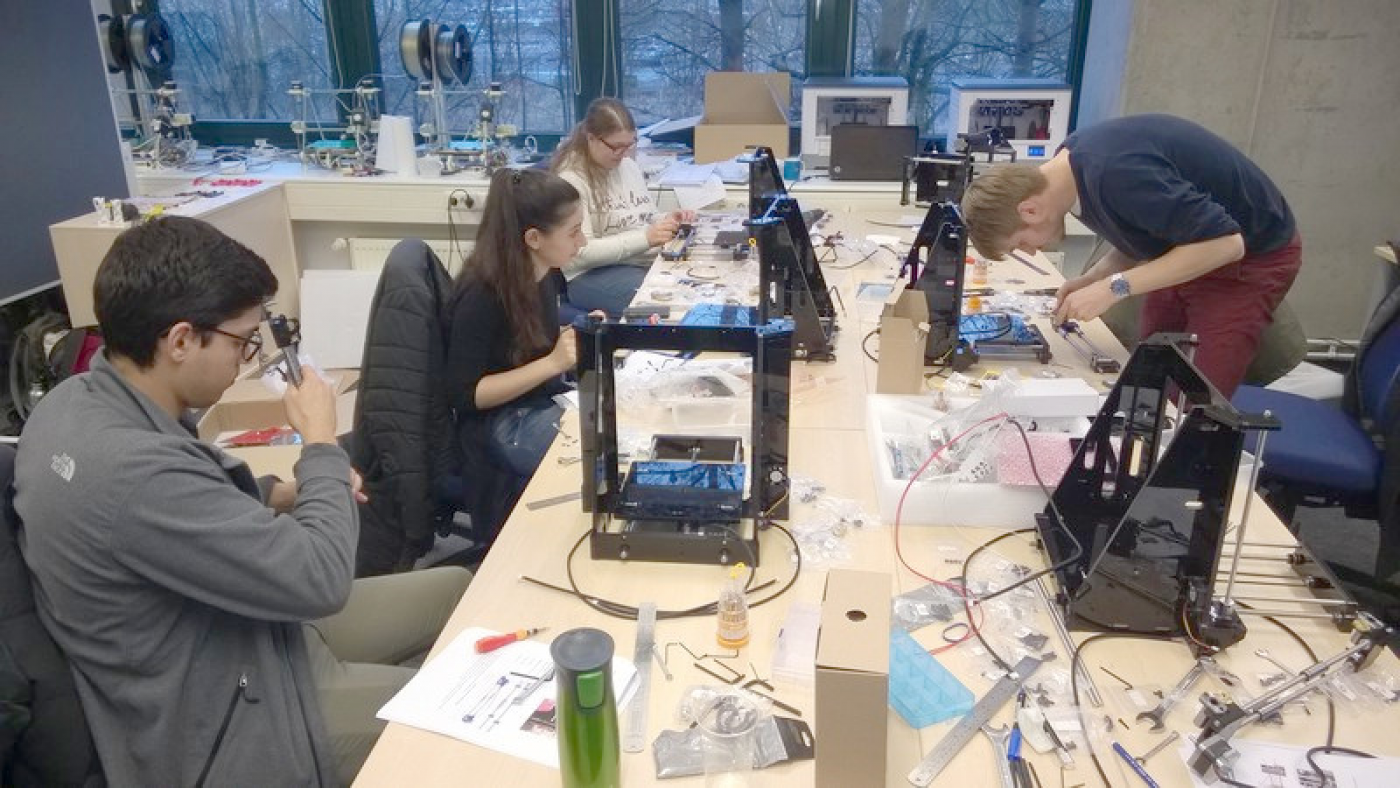
Aus der Hochschule in die Gründung
Anders Denken ist der erste Schritt, neue Ideen in tragfähige Geschäftsmodelle zu überführen der oftmals schwierigere. Mit Einrichtungen wie der TUTECH Innovation GmbH oder dem TUHH Startup Dock will die TUHH ihre Absolventen bei ihren Gründungsambitionen unterstützen. Und das durchaus erfolgreich, betont Emmelmann und nennt drei Startups, die sich im Umfeld seiner 3D-Druck-Technologieaktivitäten gegründet haben. „Die am-power GmbH & Co. KG hat sich auf Marktforschung im 3D-Druck-Umfeld spezialisiert, die Bionic Production GmbH hat sich zum Ziel gesetzt, 3D-Druck-Verfahren in die industrielle Serie zu bringen und wurde inzwischen von der HHLA übernommen und dann ist da noch ein sich gerade in der Gründung befindendes Startup, das mit seiner Software „3D-Spark“ eine smarte digitale Anwendung entwickelt hat, um automatisiert Bauteile zu identifizieren, die per 3D-Druck besser produziert werden können als mit konventionellen Verfahren.“
ys/kk
Lesen Sie auch die weiteren Teile unserer Serie:
Quellen und weitere Informationen
Ähnliche Artikel
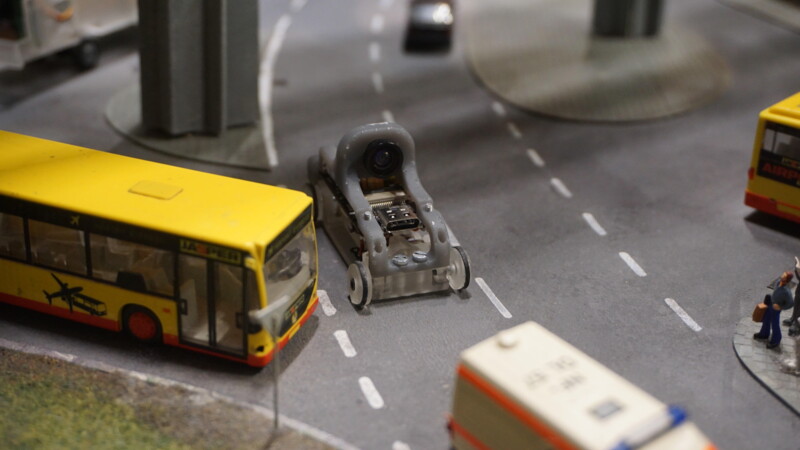
Immer mehr Einsatzbereiche für künstliche Intelligenz
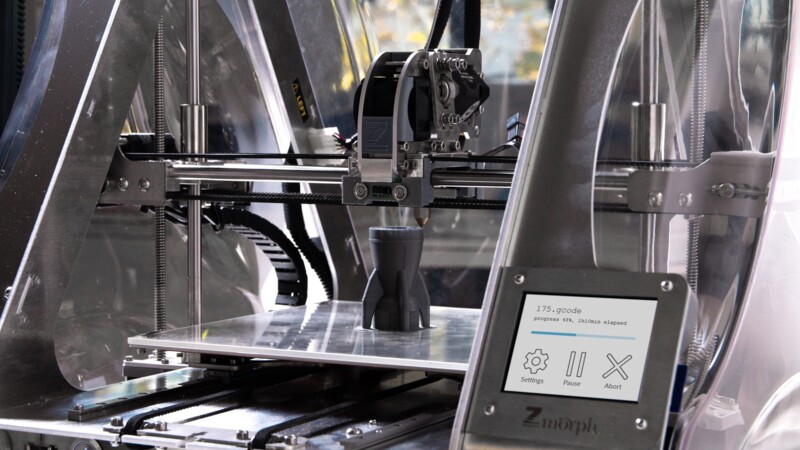
3D-Druck-Netzwerk Hamburg: neuer Web-Auftritt und neue Funktionen
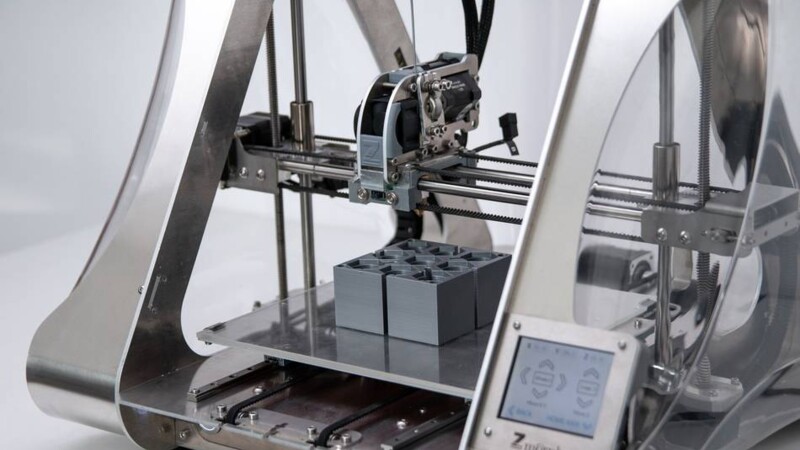
Infektionsschutz aus dem 3D-Drucker
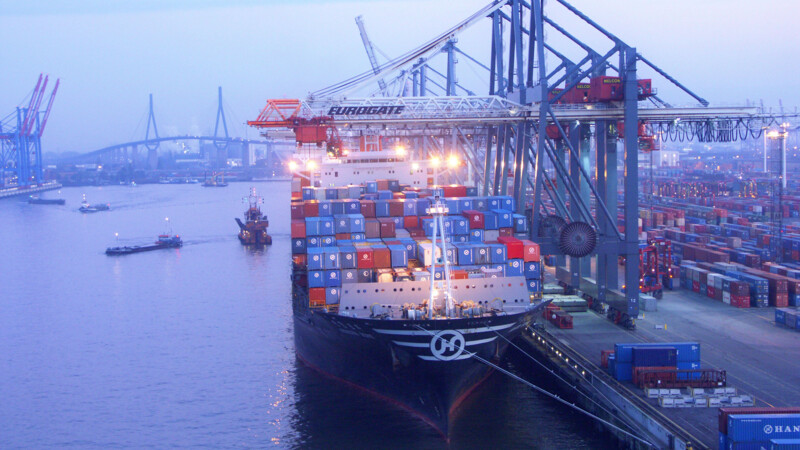