Inge Hofkens, Aurubis COO Multimetal Recycling, commented: “Partnering with Talga to close the loop for graphite from battery scrap enables us to further leverage our effective and patented battery recycling process. Given our metallurgical expertise and pioneering role, Aurubis has the potential to develop a circular solution for graphite.” Aurubis' lithium-first recycling process means valuable metals such as lithium, nickel, cobalt, manganese and graphite can be extracted from battery black mass and reused for new batteries and other products. Talga can purify the graphite concentrate supplied by Aurubis and refine it into battery-ready anode material. Hofkens added: "The aim is to make the EU independent of foreign supplies of graphite and lay the foundations for huge CO2 savings - as we have done with copper". Martin Phillips, CEO of Talga, said: “We are pleased to partner with Aurubis on the development of a commercial recycled anode product. This partnership aligns with our broader ambition to produce battery materials that enable the world’s most sustainable batteries.”
Aurubis AG and the Australian battery materials and technology company Talga Group Ltd. have signed a development agreement for a recycled graphite anode product from lithium-ion batteries, a press release said Tuesday (September 10, 2024). Tests with initial batches of Aurubis material from lithium-Ion batteries in Hamburg have yielded promising results. Talga will combine its graphite processing and anode production technologies with Aurubis' expertise in recycling complex materials. The partners hope to reach product maturity by 2025.
Closing loop for graphite from battery scrap
Huge CO2 savings potential
The EU's Critical Raw Materials Act stipulates that 25 per cent of the annual consumption of strategic raw materials, including graphite, must come from recycled sources by 2030. By the end of that year, the overall efficiency of lithium-ion battery recycling must be at least 70 per cent, according to the EU Battery Regulation. Battery manufacturers will be required to declare the origin of all materials used in battery production to meet the Environmental, Social and Governance requirements.
mm/pb
Sources and further information
More
Similar articles
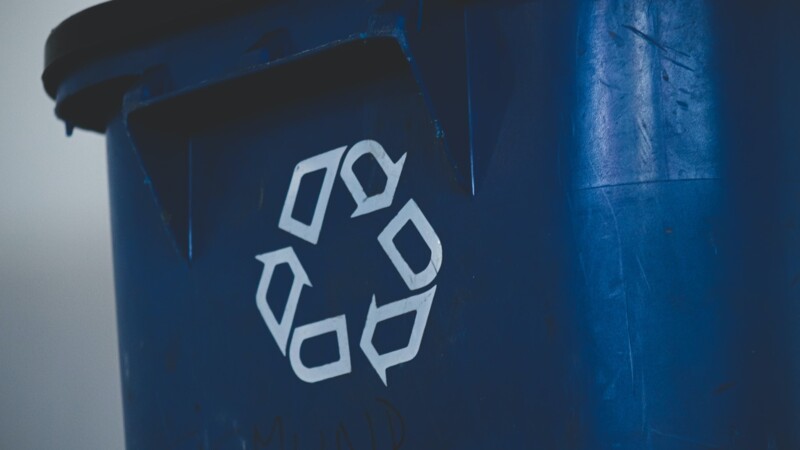
SMEs to work on circular economy in Hamburg's latest hub
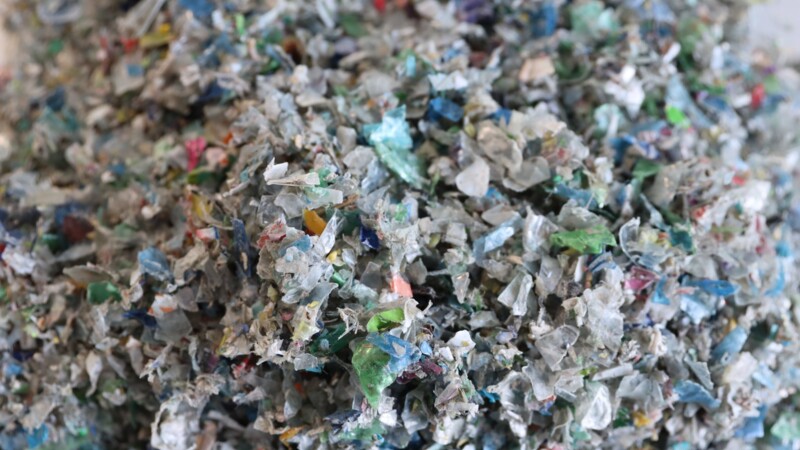
Calls for Transfer focuses on recycling chemicals for circular economy
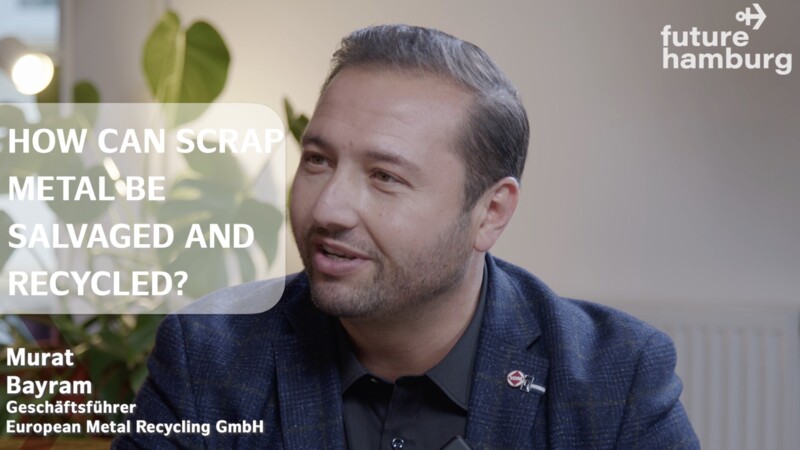